Moving to a driverless future
Automakers face a number of challenges when building an autonomous vehicle
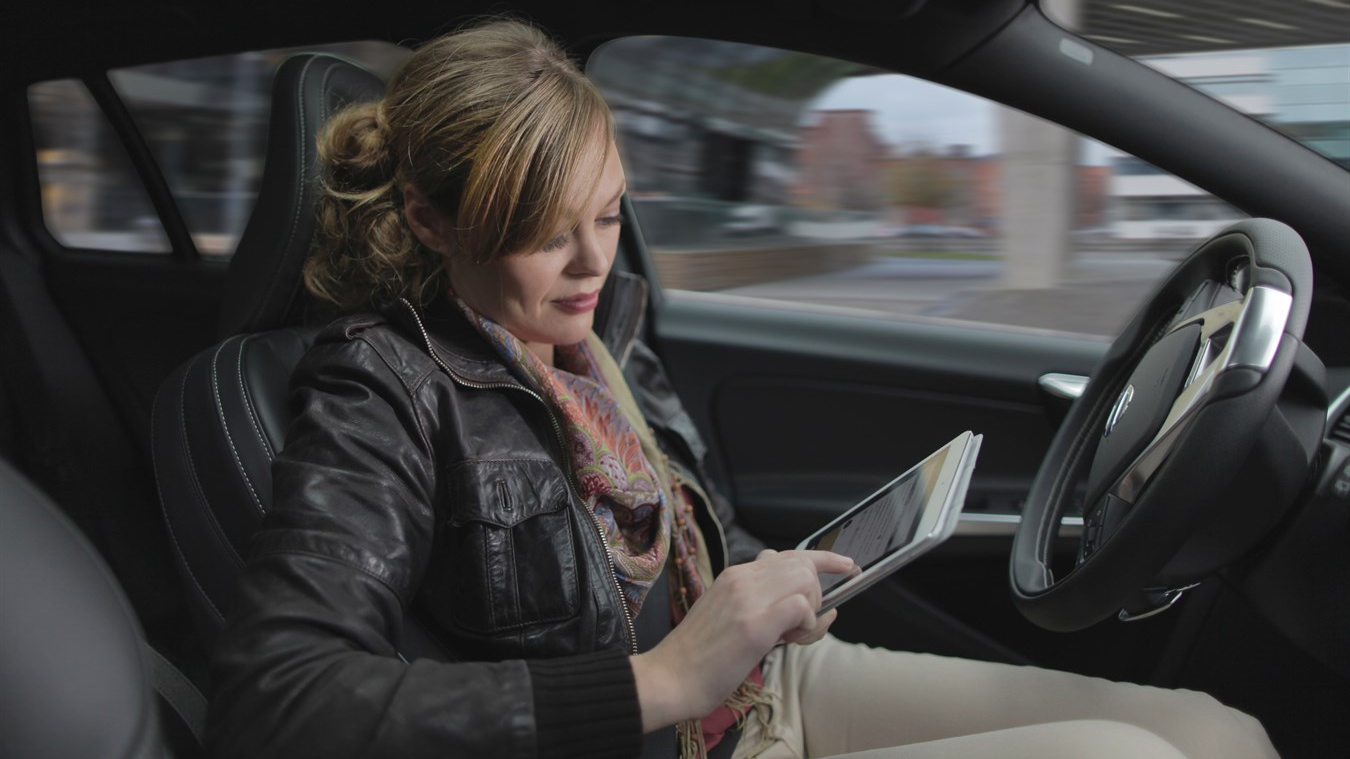
The starting point of the vehicle development process is occupant safety. Shifting responsibility from driver to carmaker to prevent accidents has a major impact on the development process. Carmakers will have to prove the thoroughness of their development processes when people get injured or killed by wrong manoeuvres from autonomously driven vehicles.
This implies automated driving systems will have to react in a safe manner to all possible traffic scenarios under any possible weather and road conditions. The technology enabling this is complex. It requires an integrated system of systems, with mechanical, electrical and software components. For an optimised design, these components cannot be treated as separate artefacts. Software and hardware need to be developed in sync to achieve required hardware costs and system performance.
A key variable in automated driving systems is sensor configuration. New sensors are being introduced at a rapid pace and more advanced sensor fusion algorithms are being developed. There is an infinite number of possible compositions to generate a 360-degree image of the environment around the vehicle, supported by different sensor types, quantities and positions on the vehicle. Sensors are typically a significant cost factor in vehicles, making configuration selection a potential market differentiator.
- Debunking the myths of driverless cars
- We need rigorous 5G testing before we get in the driverless car
- Driverless car companies need to get their maps in shape
Potentially the biggest challenge, however, is the confidence the vehicle will perform to its specifications. Not only during the development stages, but in real traffic with occupants and for many years. This requires a validation and verification process that allows for performance testing in a large number of circumstances. The process should be able to be repeated for different car evolutions over time, allowing performance comparisons for design exploration purposes.
Finally, design decisions and verification results during the vehicle development process need to be traceable. To optimise the vehicle development process, supporting integrated hardware and software development with instant optimization capabilities for sensor configurations and with a highly automated and repeatable validation and verification process is necessary. It is only scalable for mass production if the requirements, the system and simulation architectures, the models and the performance validation results are managed carefully. This would make it possible to continuously improve the product, respond to liability claims and limit redundant work by maximizing re-use of digital data.
System on chip
The time when automotive electronic control units (ECUs) are off-the-shelf components is about to end. The high compute loads and stringent requirements for low-energy consumption, combined with the specific environmental conditions, make it inevitable that specific chips will be developed for autonomous driving applications. This drives the need for the automotive industry to work much closer with the chip makers and have parallel product development processes with multiple interdependencies.
Long development cycles and the high cost of chip wafers put a stress on this relationship. However, Mentor, a Siemens business, supports the chip development process with virtual and emulated representations of early stage chip design. This enables integrated design exploration and early stage validation and verification of future system performances with realistic compute performances. Furthermore, Mentor simulation solutions can be used to optimise the thermal and durability performance of chips and systems.
Are you a pro? Subscribe to our newsletter
Sign up to the TechRadar Pro newsletter to get all the top news, opinion, features and guidance your business needs to succeed!
AD compute platform
The autonomous platform covers the control system hardware configuration. The system boundaries are the sensors on the vehicle and the actuator outputs at the vehicle’s communication bus. It is a complex assembly of electronics and wiring that requires optimised calculation time, energy consumption, thermal performance, electromagnetic capability (EMC) and multiple other attributes. Functionally, the autonomous platform translates an environment with all kind of actors into electric signals at the system outputs that make the car follow the anticipated trajectory.
Although currently automated driving solutions like adaptive cruise control, lane keeping assist and auto- mated parking systems are typically delivered as a combined product of sensors and processors, there is a strong expectation the car of the future will have a centralized architecture for a combined array of functions. A set of sensors around the self-driving car will be used to build a 360-degree representation of the environment of the vehicle that can be used for all automated driving functions. A central processor unit will run sensor fusion algorithms on raw sensor data and generate an object list of the vehicle’s surroundings.
Determining the ultimate product
To produce autonomous driving cars in large quantities, it is not feasible to add additional resources to the current vehicle development teams and simply enlarge the toolchain with additional software solutions. The requirements for energy efficiency, comfort, drivability and durability will not be reduced.
In fact, they might become more difficult with occupants doing things other than driving. Automated driving and connecting to larger networks also factors into this dilemma. Balancing the factors that influence vehicle performance in often conflicting domains is optimally done in an integrated process and toolchain. This is a key for developing shared, autonomous mobility.
Matthieu Worm, Programme Lead Autonomous Driving at Siemens PLM
Robin Van der Made, Product Manager at TASS
- Also check out the best free cloud apps for business
Matthieu Worm is the Programme Lead for Autonomous Driving at Siemens PLM.
He believe the future is bright with the birth of seamless multi-modal mobility solutions, with key roles for walking, cycling and using different means of public transport combined. Shared autonomous vehicles are a truly exciting part of that solution. He contributes to the development of this future of mobility with a balanced engineering, business and user-centered perspective.