How Gorilla Glass protects your phone
How has Gorilla Glass achieved such success?
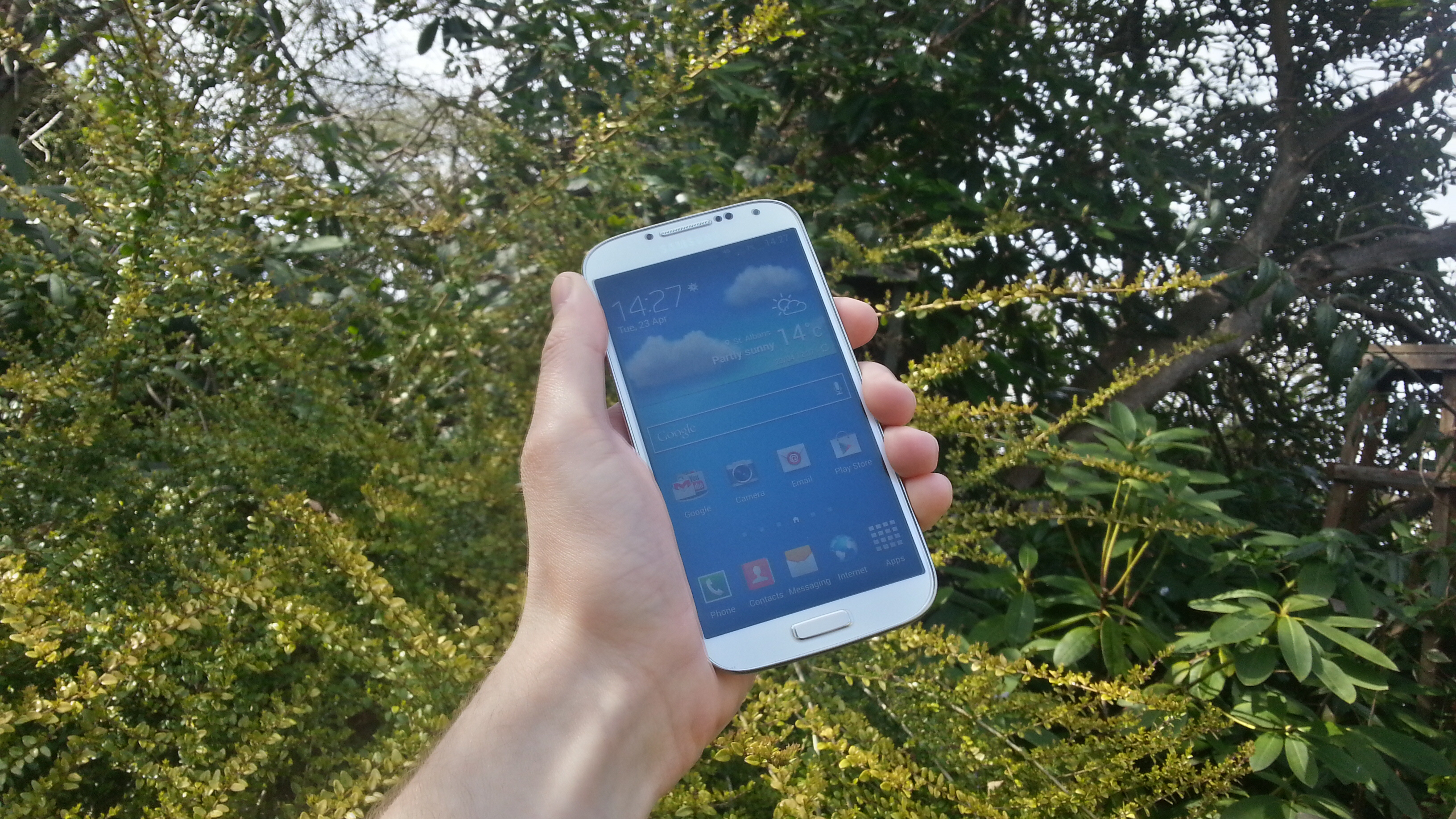
In theory, at least, using glass for the screens of mobile devices seems like a very bad idea. It's heavy, and regular wear and tear means whatever you're looking at will quickly become obscured by a mass of criss-crossing scratches and chips.
Then it will inevitably break, requiring an expensive replacement, before the whole process starts all over again.
None of this is exactly a recipe for technical success, and so it's hardly surprising that many computing hardware manufacturers initially opted for lighter, more flexible plastic screens, instead.
There are some interesting alternatives, though, and perhaps the most successful is Gorilla Glass. Produced by American manufacturer Corning Incorporated, it's a chemically strengthened glass which can be as thin as 0.4mm - less than four times the thickness of the human hair - while remaining scratch and impact-resistant.
And it's a mix which has seen the product used to protect more than 1.5 billion devices worldwide, including Samsung's Galaxy phones and tablets, Sony Bravia TVs, laptops from big names like Acer, Dell, HP and Lenovo, and even the iPhone at one point (although with neither Corning nor Apple talking, whether this is still the case isn't entirely clear).
How has one company achieved such success? It takes a little work, starting with the way the glass is formed in the first place.
Fusion draw
Gorilla Glass starts its life through Corning's fusion draw, a proprietary process which helps ensure the product is both thin and exceptionally pure.
Get daily insight, inspiration and deals in your inbox
Sign up for breaking news, reviews, opinion, top tech deals, and more.
The glass material itself is a high quality, but relatively conventional aluminium, silicon and oxygen mix - a regular alkali aluminosilicate blend - which is heated until it's molten. In the past this might then have gone through a float glass process, where it's poured onto a bed of molten metal (often tin), flattening under its own weight, then cooled until it becomes a sheet.
Fusion draw, though, sees the material poured into a long v-shaped trough called a refractory isopipe. This overflows, running down either side of the trough, rejoining at the bottom to form a single sheet of glass. This simple process helps to keep the product very pure (regular float glass has a layer of tin oxide on one side).
There's also no need for polishing, something which can itself introduce and exacerbate flaws in the glass. And the end result is a product so pristine that Corning says "a rejectable particle is comparable to a single mustard seed on a football field".
This is a great start, resulting in very thin and exceptionally clear glass. The lack of defects and unwanted particles also helps to ensure it's as strong as normal glass can be. But it is still just normal glass, unfortunately - transforming it into Gorilla Glass requires another important step.
Ion exchange
With fusion draw complete, the material produced so far is cut down to size and then placed into a 400 degree C bath of molten salt. This is all part of a process called ion exchange, a standard purification technique in many industries, but here the extreme heat is used to draw out sodium atoms from the surface of the glass, replacing them with larger potassium atoms.
Talking about swapping "smaller" and "larger" atoms may sound rather irrelevant, but it does make a very real difference. The end result is a surface coating which is far more compressed at the atomic level, making it significantly more resistant to scratches.
What's more, while regular glass has a major problem with crack propagation - the way defects will spread and grow - Gorilla Glass's state of permanent compression means the material is always pushing together, which means it's far less likely to experience any cracks in the first place.
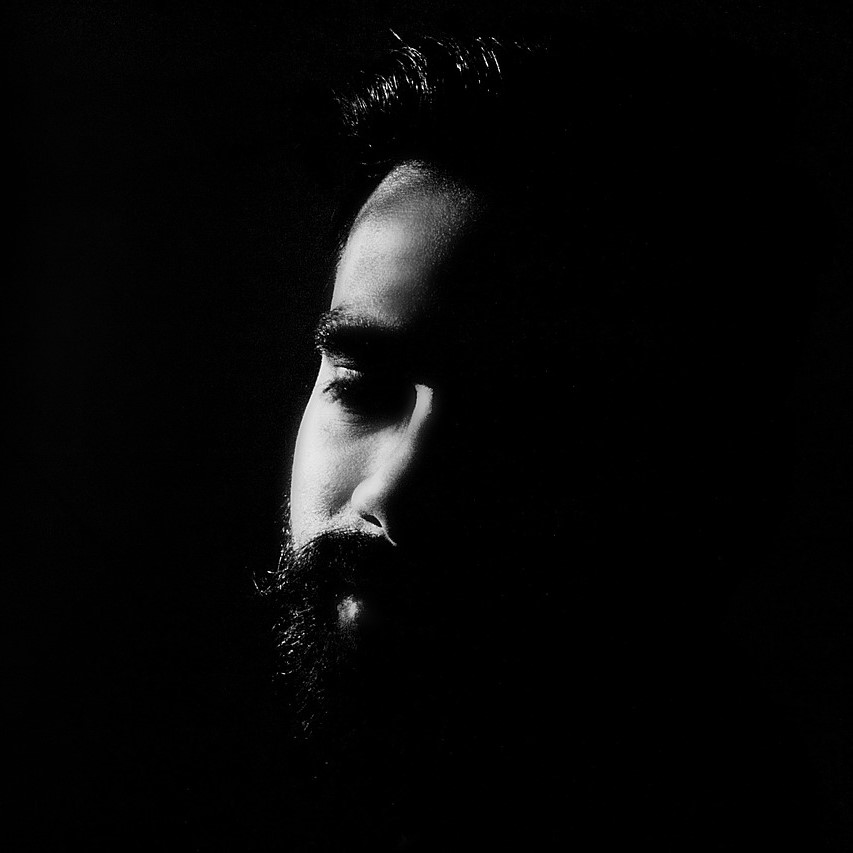
Mike is a lead security reviewer at Future, where he stress-tests VPNs, antivirus and more to find out which services are sure to keep you safe, and which are best avoided. Mike began his career as a lead software developer in the engineering world, where his creations were used by big-name companies from Rolls Royce to British Nuclear Fuels and British Aerospace. The early PC viruses caught Mike's attention, and he developed an interest in analyzing malware, and learning the low-level technical details of how Windows and network security work under the hood.