The quest for open science
We talk to Dr Richard Bowman about designing 3D-printable microscopes
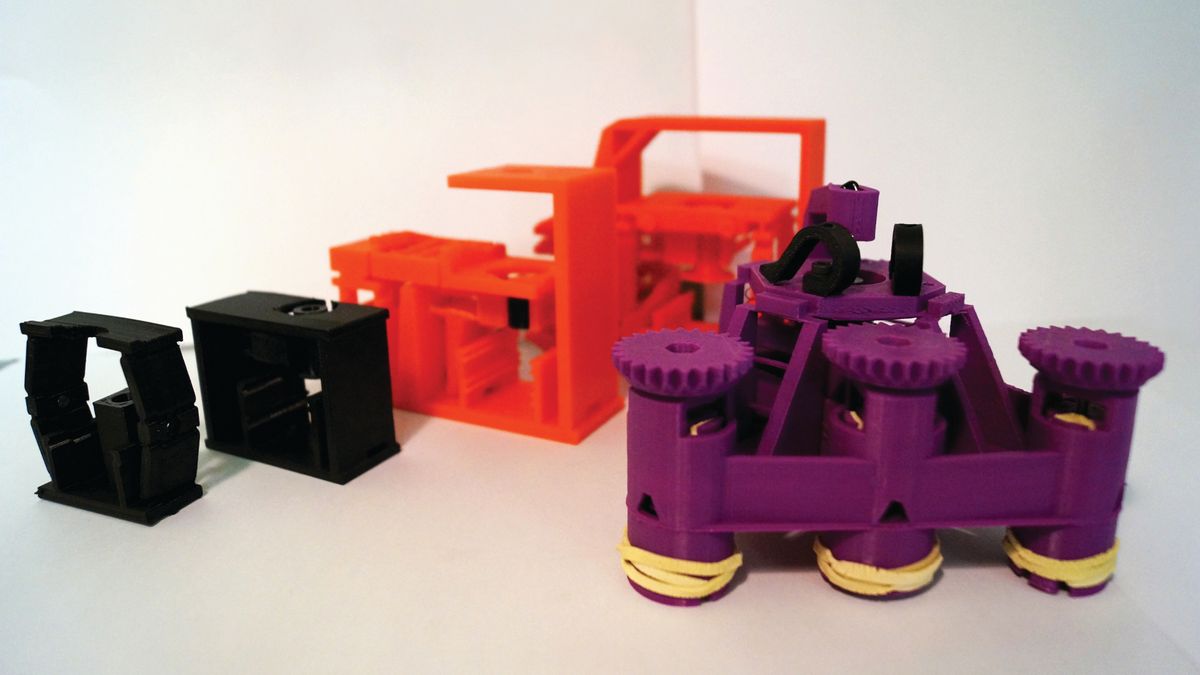
Within two minutes of talking to Dr Richard Bowman, in his lab at the University of Bath, he’s guiding me through the physics of tractor beams in Star trek. He’s using it as a simile to explain the complicated subject of optical tweezers to a stupid person.
He does so in a charming way, as someone familiar with explaining his complex field to journalists, but it’s clear why he’s a Prize Fellow and Royal Commission 1851 Research Fellow – his explanation ends with our imaginary tractor beam melting an object it’s trying to move before Bowman shrinks this entire sci-fi example down to demonstrate how he’s used laser beams in his past work to move tiny objects.
On the face of it, Dr Bowman’s story is that he’s on a three-year project to build a general-purpose 3D-printed microscope, but his ambitions are bigger and, ultimately, he wants to create 3D-printable ‘building blocks’ that others can use to make affordable, new experimental apparatus. “Opening up hardware means more people have access to it,” says Dr Bowman.
“Personally, I’m keen on pushing the hardware to be of a quality that I would not be embarrassed to use in a well-funded university research lab. There’s also a big push to having stuff you can make at home, and so making scientific research more accessible means that schools, science clubs and makerspaces can start doing really interesting scientific stuff. [...] The more of the public that gets involved in science the better, as far as I’m concerned.”
As well as being a co-founder of WaterScope, a project developing faster and easier-to-use water-testing field kits that use a microscope he designed, he’s a passionate advocate for open hardware and works with organisations like GOSH (the Gathering for Open Science Hardware).
The journey begins
Dr Richard Bowman’s journey towards open hardware began while working on optical tweezers for his PhD at the University of Glasgow. There he experienced first-hand the cost of custom scientific instruments. A research-grade microscope “with all the bells and whistles and a motorised stage”, says Bowman, will set you back £30,000 to £40,000. “Then you void the warranty by ripping out most of the complicated optics from inside of the microscope and replace it with your own stuff.”
The situation was frustrating and not as efficient as it could be but then – at Queens College, Cambridge University, where he was working in a nanophotonics group and dealing with automated microscopy – he began meeting people interested in open source hardware: “I met someone who was building a 3D-printed microscope and it looked a lot like this,” says Bowman pointing to a RepRap 3D printer nearby.
Are you a pro? Subscribe to our newsletter
Sign up to the TechRadar Pro newsletter to get all the top news, opinion, features and guidance your business needs to succeed!
That was Alexandre Kabla and a project called OpenLabTools. “The goal is to be self-replicating and to print as many of its parts as is possible, but in practice you found that most of it isn’t printed,” says Bowman, and that was the spark that got him thinking: “I was curious just how much of a microscope you could print.”
Bowman shows us one of the first microscopes he printed: “This,” he says, “will turn a Raspberry Pi camera into a microscope.” It’s a tiny black extension tube (pictured in the image at the top of the page), which photographers have used for a long time: “On your webcam you have a tiny little shiny silicon sensor and the pixels on there are very small [...]. I think it’s 1.1 micron [across] for the version 2 Raspberry Pi Camera Module. So this lens that forms an image on the sensor is, in fact, a microscope objective, because it’s focusing the light down to a spot not much bigger than a micron and for linear optics at least, [...] you can reverse the light path and it does the same thing.”
Dr Bowman explains that if he unscrewed the lens and pointed it at the object he wanted to look at – putting the lens some distance away from the sensor – it would function as a microscope.
Mechanical matters
Surprisingly, the difficult aspect of microscopy isn’t the optics but the mechanicals. Working with objects that are millionths of a metre across requires a very high-powered microscope to see anything and at that point the depth of focus of your microscope is less than a micron. Using a larger motorised model of his 3D-printed OpenFlexure microscope (pictured above), Bowman demonstrates the problem. “If your sample wobbles even by a micron [...], a hundredth of the width of a human hair, your whole experiment is ruined.”
The expensive part for serious science work, then, is building a mechanical stage for fine control of what you want to look at. “A Raspberry Pi Camera Module is £25, but the mechanical stage might then cost you £1,000 or easily more than that.” So Bowman began a process of researching and prototyping mechanical stages. You can see some of the iterations pictured in the image at the top of this page: the key step up, which Bowman describes as a “middle of the night” epiphany, was having the sample sit on a table (the last red microscope in the top image) that has legs designed to bend in a way that allows for the crucial focus control and movement on the X and Y axes.
Ultimately, Bowman’s microscope design is a complicated structure and impossible to machine: “You can print it layer by layer, but you can’t machine it,” says Bowman, smiling. “You couldn’t injection-mould it either.”
Bowman’s larger microscope with a motorised stage, which he demoes to us, uses Python scripting for enabling the user to move the field of view around the slide. The aim is to add more features such as auto-focus and the ability to stitch all the images back together for a digital representation.
Chris Thornett is the Technology Content Manager at onebite, editor, writer and freelance tech journalist covering Linux and open source. Former editor of Linux User and Developer magazine.