How 3D printers work
Check out the latest technologies being used for 3D printing

How 3D printers work
Over the last couple of years, we've seen a wide array of 3D printers such as the Lulzbot Mini being made available to consumers. The amazing thing is that in reality, most consumer-grade 3D printers are surprisingly simple beasts and there isn't as much to them as you might think.
In fact, a basic 3D printer is not much more than a glorified stationary robot with a brain made from low-cost 8-bit microcontroller technology that's been around for 20 years or so.
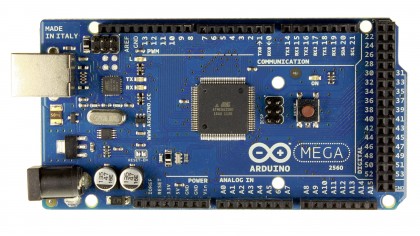
The brains of Arduino
In 2005, long before Raspberry Pi, a couple of Italian engineering lecturers came up with the idea of creating a small computer board that was cheap and easy to use, allowing anyone to mate digital computing with real-world components like motors, sensors, lights and switches. It's called 'Arduino', it's taken the world by storm and it's based on a microcontroller technology created back in 1997.
You no doubt know about 'microprocessors' that power your PC, phone or tablet – but a microcontroller is different. Whereas a microprocessor needs a mountain of extra components to handle memory and storage and talking to the outside world, microcontrollers have small amounts of all that built right into the chip.
What's more, using clever technology called 'analog-to-digital conversion', they can listen to the outside world as well. They're used in a myriad of single-function or 'embedded' applications, including drones, as we saw from last month.
The vast majority of consumer-grade 3D printers have an Arduino Mega-class microcontroller at their heart and you'll find Arduino Mega board clones on eBay that are relatively cheap.
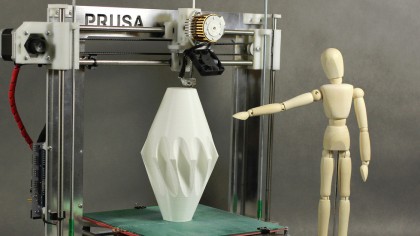
Hot-end
The pointy-end of a 3D printer is actually the 'hot-end' or extruder and combines a motor drive to push filament through at a user-settable rate, with a heating element turning the plastic filament into a soft, molten goo at the nozzle.
Typically made from brass, the hot-end has a small reservoir where filament is heated via a tiny heater (an electronic component called a 'resistor') up to as high as 250℃ (482℉).
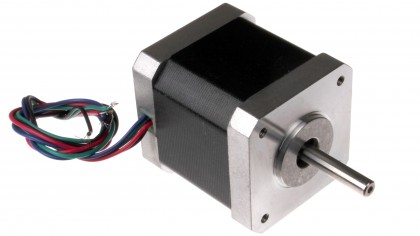
Stepper motors
But the key to 3D printing is maneuvering that hot-end filament nozzle to the right location at the right time, delivering the molten plastic filament to build the 3D object one layer at a time.
The job of doing the maneuvering falls to a special type of motor called a 'stepper motor'. Ordinary motors are pretty simple gadgets – you apply an electrical voltage to their terminals and they spin.
With some, you can swap the wires (called 'reversing the polarity') and the motor spins in the opposite direction. Stepper motors, however, are completely different – using multiple electromagnets, a stepper motor allows rotation in precision steps, as precise as 200 steps per revolution.
The most common types used in industry are known as NEMA (National Electrical Manufacturers Association) motors, which have standardised physical dimensions making them easier to work with.
To make a 3D printer, you need at least four stepper motors – one for each of the three axes of movement, plus one to control the flow of filament. However, most designs will use five, with two for the vertical or 'Z' axis.
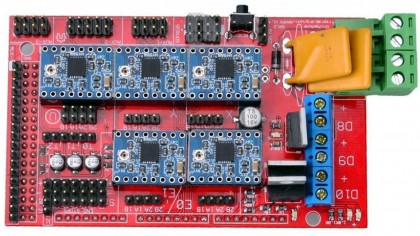
RAMPS
The problem with the Arduino Mega board however, is that it doesn't have the electrical brawn to drive a NEMA-17 stepper motor on its own, so it's commonly used with a series of stepper motor driver chips that provide sufficient muscle to power the motors.
The 3D printing community has created a special add-on board or 'shield' for the Arduino Mega that incorporates these driver chips called RAMPS (RepRap Arduino Mega Pololu Shield). It's a general-purpose 3D printer power board designed to handle a wide-range of 3D printer designs.
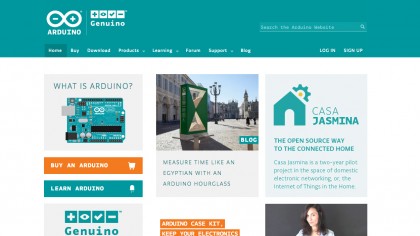
Firmware
Consumer-grade 3D printers connect up to a PC (or phone, even) via USB, so essentially, they're just a USB peripheral device.
But in order for this collection of hardware bits to do anything, the Arduino Mega microcontroller needs to be loaded with firmware that turns the printing instructions from the PC into actual movement and flowing filament from the printer's other components. Marlin is one of the most popular firmwares and can be loaded onto an Arduino Mega without too much fuss.
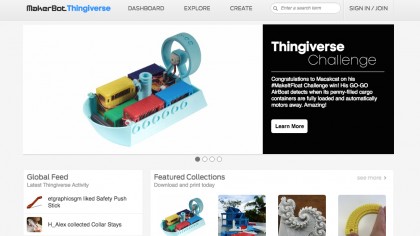
Software
On the PC side, you need software to turn 3D designs into physical objects. Software such as Repetier-Host takes stereolithography (STL) files you download from Thingiverse, slices them into rows and feeds each row in turn to the Arduino Mega board inside the 3D printer.
Repetier-Host is free and available for Windows, Mac OS X and Linux. You can also print direct from your smartphone with GCodePrintr on Google Play.
Other alternatives include the new MatterControl Host, again for Windows, Mac OSX and Linux and Ultimaker's Cura.
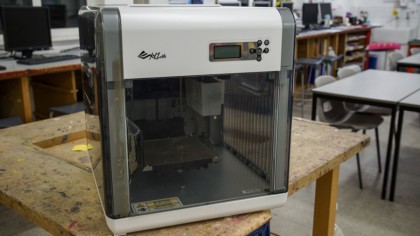
Innovations in 3D printing
It's not surprising that governments are looking to the likes of robotics and 3D printing as future economic drivers – to use a well-hackneyed phrase, they are 'disruptive technologies', technologies that are changing the way we do things.
Still, it'd be fair to say 3D printing hasn't exactly grabbed the average person enough to go and buy one. But in just the last few months, 3D printing has made some pretty amazing leaps forward in everything from aeronautics to health, including some impressive home-grown wins.
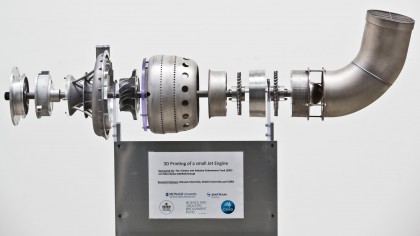
3D-printed jet engine
Countries are becoming increasingly interested in the technologies used for 3D printing. For example, In late-March this year, Australia announced itself as a centre of 3D printing innovation when Monash University, in combination with the CSIRO and Deakin University, unveiled the first 3D-printed jet engine at the Avalon International Airshow.
The team, led by Monash University Professor Xinhua Wu, was given a working gas-turbine engine, used as an auxiliary power source in 'Falcon 20' aircraft from French aerospace maker Microturbo.
The Monash team pulled apart the engine, 3D-scanned each component and using the latest tricks in their kitbag, quietly printed off two more. Monash has since spun off a new company, Amaero Engineering, to commercialise the technology and give local companies a chance to benefit.
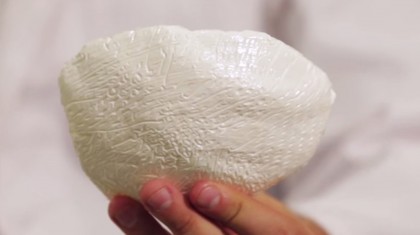
Bone replacement
But printing jet engines isn't the only thing Australia seems to be pretty good at. Not to be outdone, Sydney University's Faculty of Engineering has begun trialing 3D printed bone implants in patients with severe head trauma – with considerable success.
The new technique, called 'rapid templating cranioplasty', has been developed in conjunction with neurosurgeons at Liverpool Hospital in New South Wales. It uses a patient's previous radiography scans to create a sterilised, patient-perfect implant printed from a polymer-based bone cement.
The benefits for patients and surgeons are that it's not only cheaper, it's also stronger, faster to make and safer for patients than previous methods.
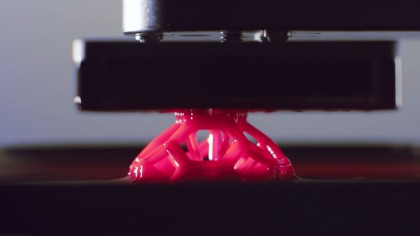
Super-fast 3D printing
One of the likely reasons for the apparent lack of consumer interest in 3D printing has been the slow print speeds of consumer-grade FDM (fused deposition modelling) technology. However, in the last few months, there's been something of a breakthrough in stereolithography (SLA) 3D printing.
California-based Carbon3D has developed a new technology called CLIP (continuous liquid interface production) that claims to deliver print speeds of between 25 and 100 times faster than current SLA tech.
Stereolithography uses ultraviolet (UV) light to cure polymer-based resins into 3D objects, but whereas a particular object using traditional SLA tech might take near-on 12 hours to print, the same job can be done with CLIP in under seven minutes, an astonishing improvement.
And Carbon3D is talking about commercial-quality printing at that speed, which is likely to open up a raft of new opportunities in prototyping and small-run industries.
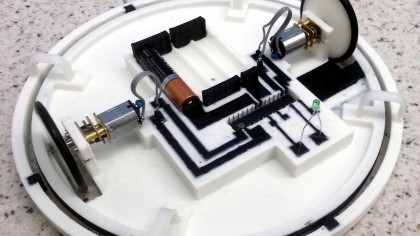
Printing electric circuits
One of tomorrow tech's great goals is the ability to do away with comparatively expensive and restrictive electronic circuit boards and direct-print electrical circuits using 3D printing techniques. Previously, filament conductivity was a fairly low 10,000ohms per centimetre, too low for much else other than very low-power sensors.
Today, US start-up Functionalize has joined forces with filament maker ProtoParadigm to create a new filament called 'F-Electric' with a much-improved conductivity of 0.47-ohms per centimetre.
Still, with circuit boards using almost-pure copper having 0.00001ohms-per-centimetre conductivity, conductive filament still has a fair way to go yet to reach those numbers. But the improvements made in just the last few months suggest we haven't reached the end yet.
At US$142 for about half-a-kilogram, F-Electric isn't exactly cheap, but with quite reasonable conductivity, there's potential for numerous applications, particularly as printing speeds increase. The inventor of the RepRap open-source 3D printer project, Adrian Bowyer, plans to use the material to fully 3D-print an Arduino-style robot, circuits and all.
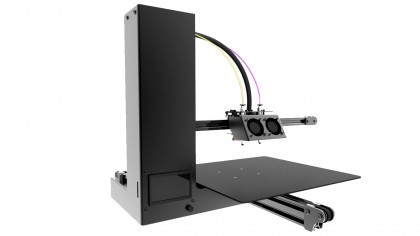
Budget 3D printers
Meanwhile, waves of consumer-grade 3D printers keep coming. You're probably asking yourself 'why do I need a 3D printer', but you could be soon using one in study, work, or just be the recipient of the output from one, through medical prosthetics or traveling around the globe.
One of the latest consumer models, due to hit September this year, is the X3D Machines' Genesis series. Starting life as almost all 3D printers seem to – on Kickstarter – early-birds could pick up the stylish single-head Genesis Uno for US$199 plus shipping. With a decent 9 x 9 x 12-inch build volume, LCD panel and aluminium chassis, the Genesis Uno looks as though it could wipe the floor with some post-$1000 printers currently available.
And it's not even the cheapest – the new Tiko is another Kickstarter alumni, featuring the popular tri-carriage 'delta' design and a US$179 pledge price. With a unibody frame and enclosed design, Tiko will handle a wide array of filaments including PLA, ABS and Nylon. It's now had over US$1.2million in backing at time of writing.
Then there's Flux, which received more than US$1.6million in support from Kickstarter and combines a delta-style 3D printer with built-in 3D scanner and laser engraving. Early-birds grabbed it for as little as US$599 plus shipping.
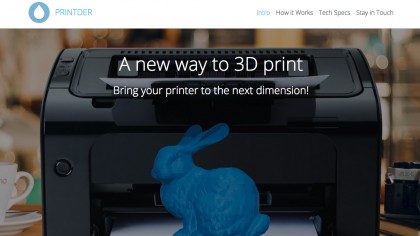
Turning a 2D printer into 3D?
But one idea that just may turn heads is Printder, which claims to turn an ordinary sub-$100 2D printer into a 3D printer.
Like any 2D printer, it works by ink and paper, but how it creates 3D objects sounds quite clever. According to the website, each sheet of the specialised paper becomes a 3D layer, with the ink printed acting as a glue. Once you've printed out all of the page layers that make up your object, you take the output paper tray and whack it in the oven for 15 minutes to allow the ink to fuse the pages together (there's no smell, they say). After allowing it to cool, you dunk the whole thing in water, the excess paper dissolves and you're left with your 3D object.
With an A4 inkjet printer, you'd have an A4-size build area (30 x 21centimetres) up to a 'height' of six inches (15centimetres).
It sounds ingeniously simple, but there are still plenty of unknowns at time of writing – such as the printers it'll work with, the cost of the ink and cost of the special dunk-and-disappear paper. We're also wondering how the duty-cycle of most budget printers will cope with the workload. Still, we're intrigued by this one, so we'll keep an eye on it.