Industry 4.0: an industrial evolution, rather than a revolution
The connected, intelligent factories of the future
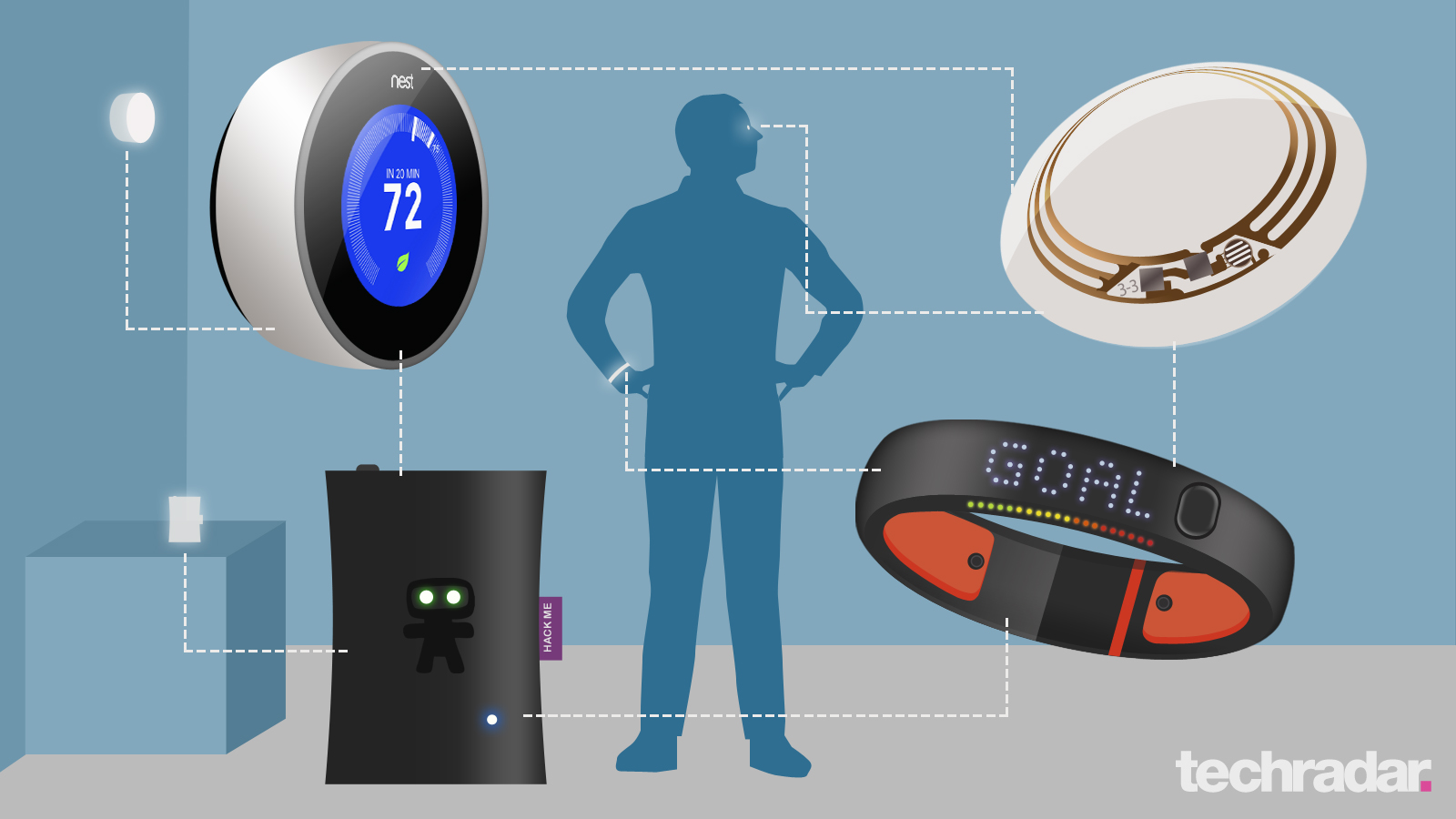
A quick history question: how many industrial revolutions have there been? Most of us will recall school lessons imparting details of the shift from farming to industrial production. However, since then there has been a second industrial revolution which introduced mass production with the help of electric power, followed by the IT revolution that saw the advent of electronics and technology to further automate production. And we now face the dawn of a possible fourth industrial revolution as digitisation takes hold.
What makes digitisation so special? It opens up new ways to respond efficiently to customer needs with methods that can fix problems (almost) automatically. How is this done? By converging a specific set of new technologies and strategies, grounded in a customer-centric approach.
Firstly, the development of the Internet of Things and cyber-physical systems such as sensors and wearable technology has enabled machines, computers and even data itself to have an active role in the manufacturing and production processes.
Secondly the development of big data and powerful analytics means that these systems can process huge data sets and that information can be quickly translated to intelligent courses of action.
Lastly the communications infrastructure on which these "conversations" rely has become so secure that it can be trusted with business critical aspects such as production.
In typical fashion, this amalgamation of technology and business strategy has been given a shiny new name: Industry 4.0.
The name is already going global. In Germany, Industry 4.0 includes an initiative that promotes the computerisation of traditional industries such as manufacturing. In the United States, the Smart Manufacturing Leadership Coalition (SMLC) is a non-profit organisation of manufacturing practitioners, suppliers, and technology companies, along with manufacturing consortia, universities, government agencies and laboratories with a similar objective.
Are you a pro? Subscribe to our newsletter
Sign up to the TechRadar Pro newsletter to get all the top news, opinion, features and guidance your business needs to succeed!
Not just another label
From a business perspective, it is critical to understand that this is not a new technology or even a new business discipline in itself. It is more an approach to enable results that were impossible a decade ago. Companies do not ask specifically for "Industry 4.0 solutions", and the technology industry should not want to create such a label. Rather there needs to be an Industry 4.0 approach to solving customer demands as the new technology enables.
For example, let us suppose the "brief" is to increase the speed of business processes and to run semi-autonomous processes that can produce more efficiently. Or to deliver customised or specialist products in small quantities, without risking lost productivity and higher production costs.
For either set of demands, it is easy enough to identify elements such as communication between machines, the analysis of large volumes of data in order to optimise the processes and the need for secure links between design and production. What is needed however is a holistic strategy to pull all this together, with modern software applications able to span these connections and deliver the data needed for analysis.
There are two notable pressures on the development of this software. Firstly, speed: the timeframes for innovation are getting shorter. Consequently this software must be developed and evolved faster than ever. Secondly, complexity: due to the increased automation and networking, every process has far more moving parts. As a result the software must be flexible.
Not just another technology
From a business perspective there is also the need to recruit, retain and develop a specific set of collaborative problem-solving skills. If Industry 4.0 is grounded in identifying customer requirements and the issues they face, it becomes an inherently collaborative process to solve those challenges. Sadly many of those skills are still very difficult to find.
Broadly speaking there are three categories of these challenges: market, business and technology. Market challenges could include the entry of a new competitor or a new geography opening up. Business challenges are typically more "internal" – a change to the business model, or threats and opportunities presented by partners and suppliers. Challenges presented by technology itself are simply a consideration of the benefits that can arise from better management of the digital components of existing systems.
That management is dependent upon the solid, flexible integration of systems. A standards-based framework that provides the technological foundation to build business processes and workflows throughout and beyond the Smart Factory is critical. Likewise, the interface between people and technology has to be quick, intuitive and reliable.
In addition, change management will be a vital part of Industry 4.0 success. As employees' areas of responsibility change from the management of standard tasks to tracking automated processes and detecting errors and fixing them, the ability of staff to solve complex problems will demand substantial re-training.
These are challenging goals. Thankfully Industry 4.0 is less of a fourth revolution and more of an evolution in many small steps that will truly change how manufacturing and industry does business.
- Paul Carreiro is executive vice president and managing director, EMEA, at Infor