I saw how Samsung builds its Samsung Galaxy S23 Ultra and it blew me away
Inside Samsung’s incredible Gumi Smart City
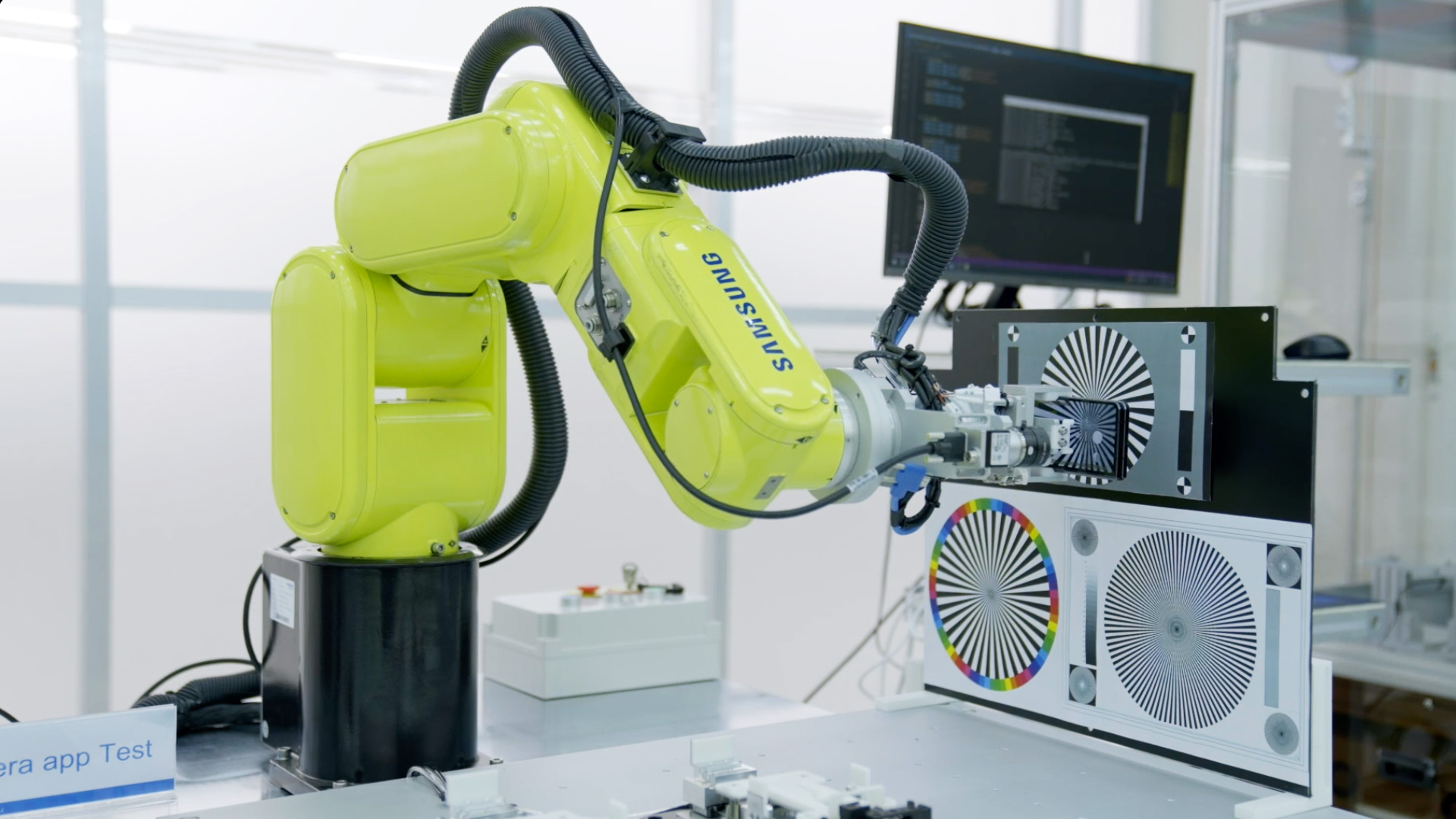
Phone companies like Apple and Samsung are not in the habit of showing you how the sausage is made. Smartphone design and manufacturing details are typically closely-guarded secrets, not readily shared with the public much less tech journalists like me. Until now, that is.
Last week I traveled to South Korea, the home of Samsung, to see for the first time how Samsung designs and builds everything from the new Samsung Galaxy Z Flip 5 and Galaxy Z Fold 5 to its powerhouse Samsung Galaxy S 23 Ultra.
For its annual Samsung Unpacked event, Samsung took me behind the scenes and into the heart of its phone manufacturing process. I’ve been reviewing smartphones now for 20 years and this is the first time I stood before the production line and watched as not one, but dozens of Samsung Galaxy S23 Ultra were built, programmed, tested, and packaged. It’s quite stunning.
Despite Samsung’s transparency, though, it would not allow me or any of the other assembled tech journalists to photograph the process. I have some images supplied by Samsung that will provide a glimpse of the wonders I witnessed. It’s an incredibly complex yet sensible and highly efficient system, one that may change the way you look at your smartphone.
To see the production line for myself, Samsung drove me three hours away from the crowded city of Seoul, past farmland, and through innumerable tunnels to Gumi, a factory city (Samsung calls it a “Smart City”) where 16% of its 407,000 residents work for Samsung. On the day I arrived, it was one of historic, record-breaking heat – the hottest all year in what is traditionally Korea’s hottest city. During my visit, our phones were repeatedly pinged with excessive heat warnings. A stroll between the campuses’ major buildings required an umbrella to shield us from the almost unbearable heat and intense sunlight.
Inside Building B, though, all was cool, calm, and humidity controlled.
Samsung’s been producing cell phones at Gumi since 1988, adding a second campus in 1996 for a total of five major complexes. Gumi produces both electronics and smartphones, of which it manufactures roughly 270 million units per year. Earlier this month, they surpassed 6 billion products. As we prepared to enter one of the main lines, a production manager proudly gestured to a wall-mounted green LED sign that keeps count and displayed the 6-billion-plus figure. Throughout my tour I got the sense that Samsung employees are tremendously proud of Gumi’s accomplishments.
Get daily insight, inspiration and deals in your inbox
Sign up for breaking news, reviews, opinion, top tech deals, and more.
Samsung builds millions of phones each year in Gumi, even as the majority of smartphone production is taking place in Vietnam and India. But what I saw in Gumi is a template for how Samsung builds its Galaxy handsets around the world.
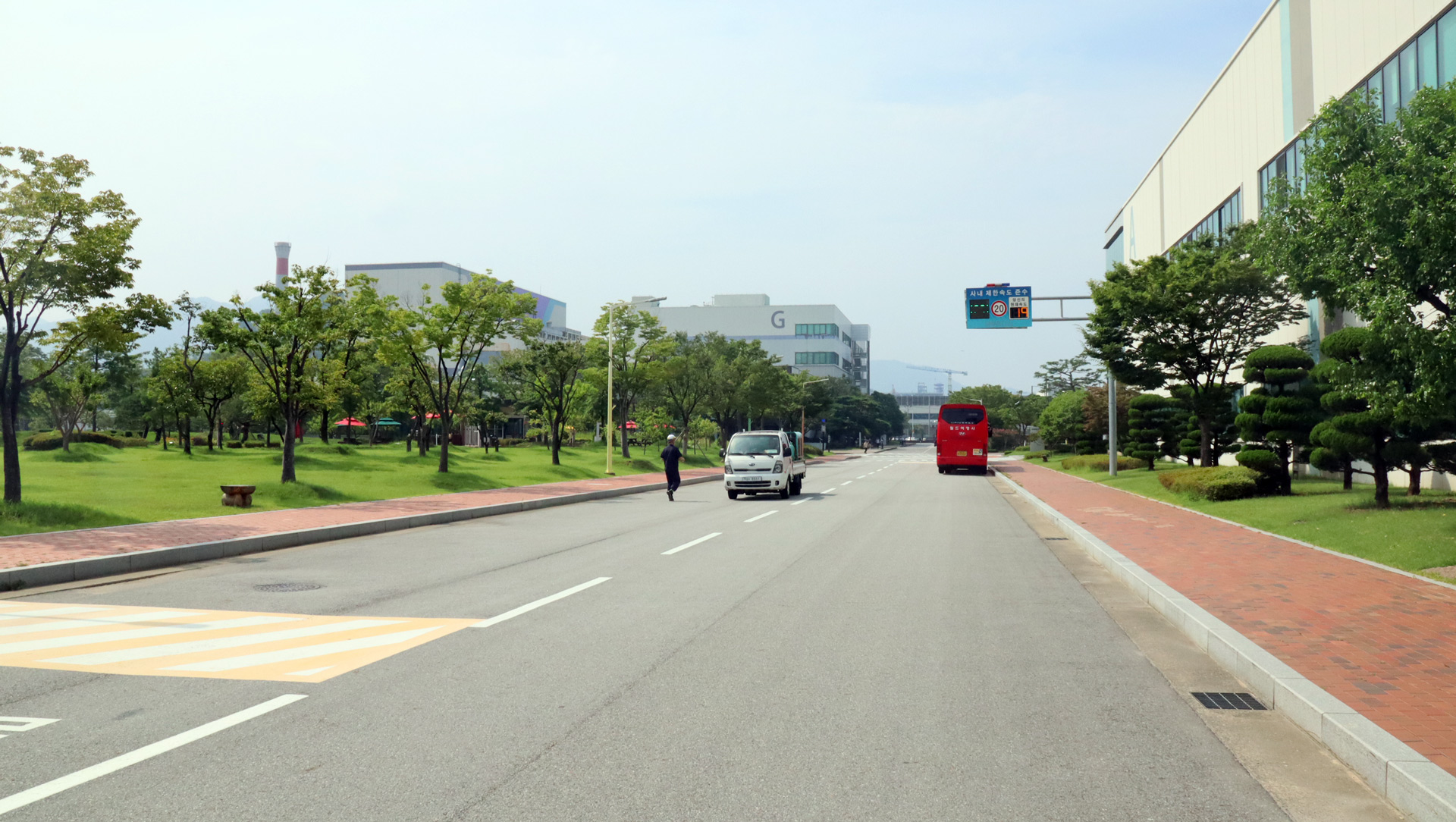
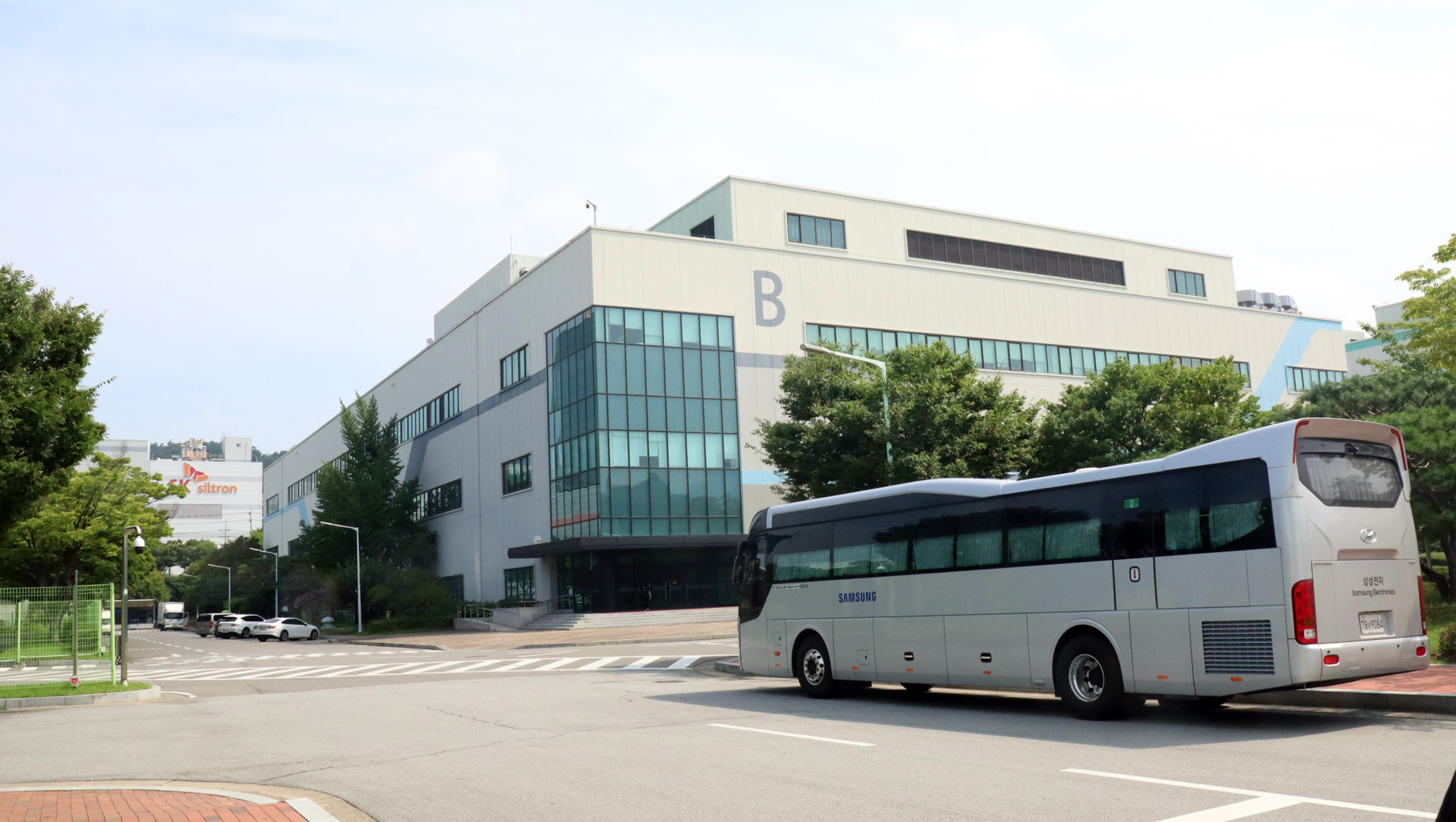
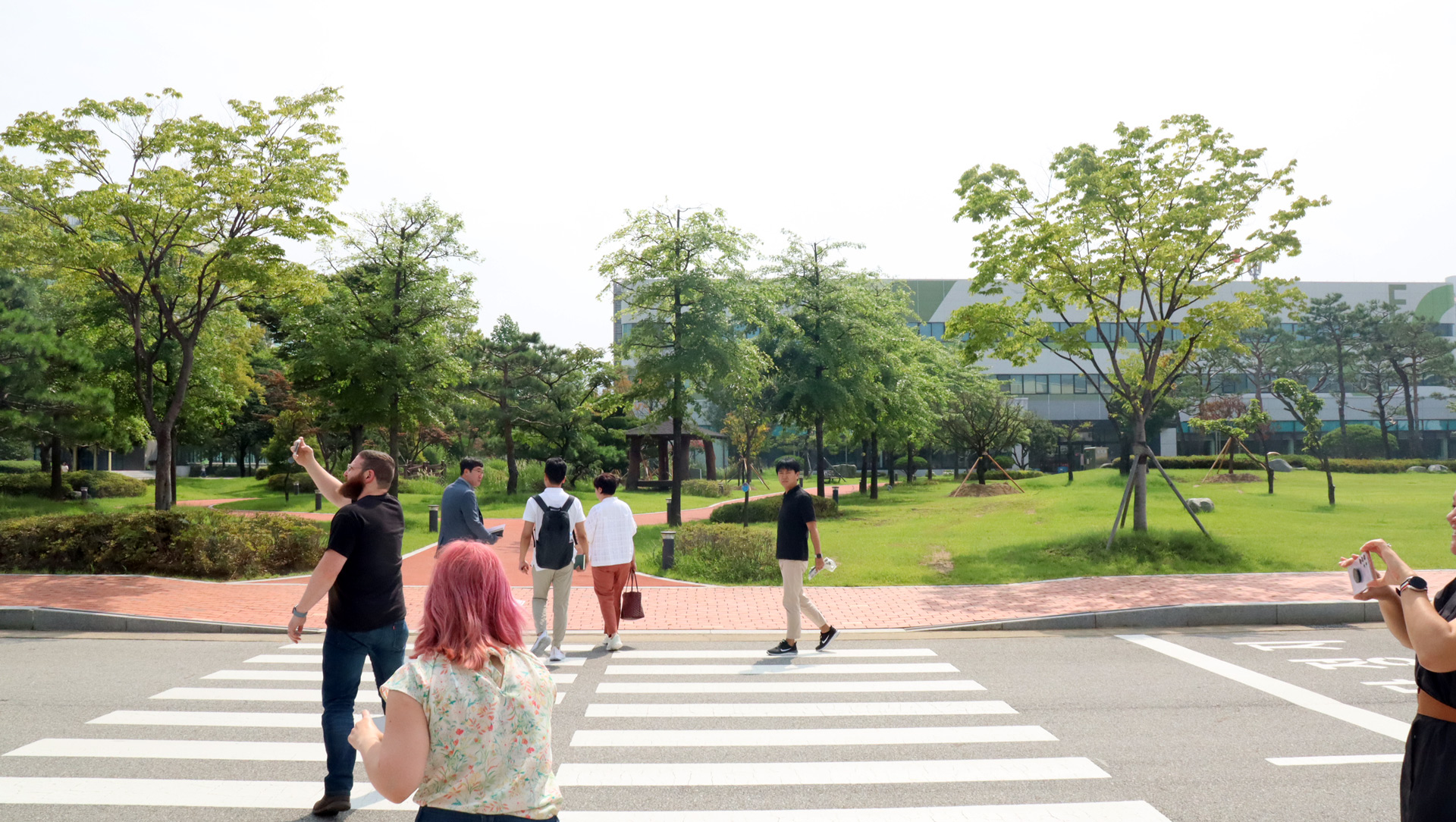
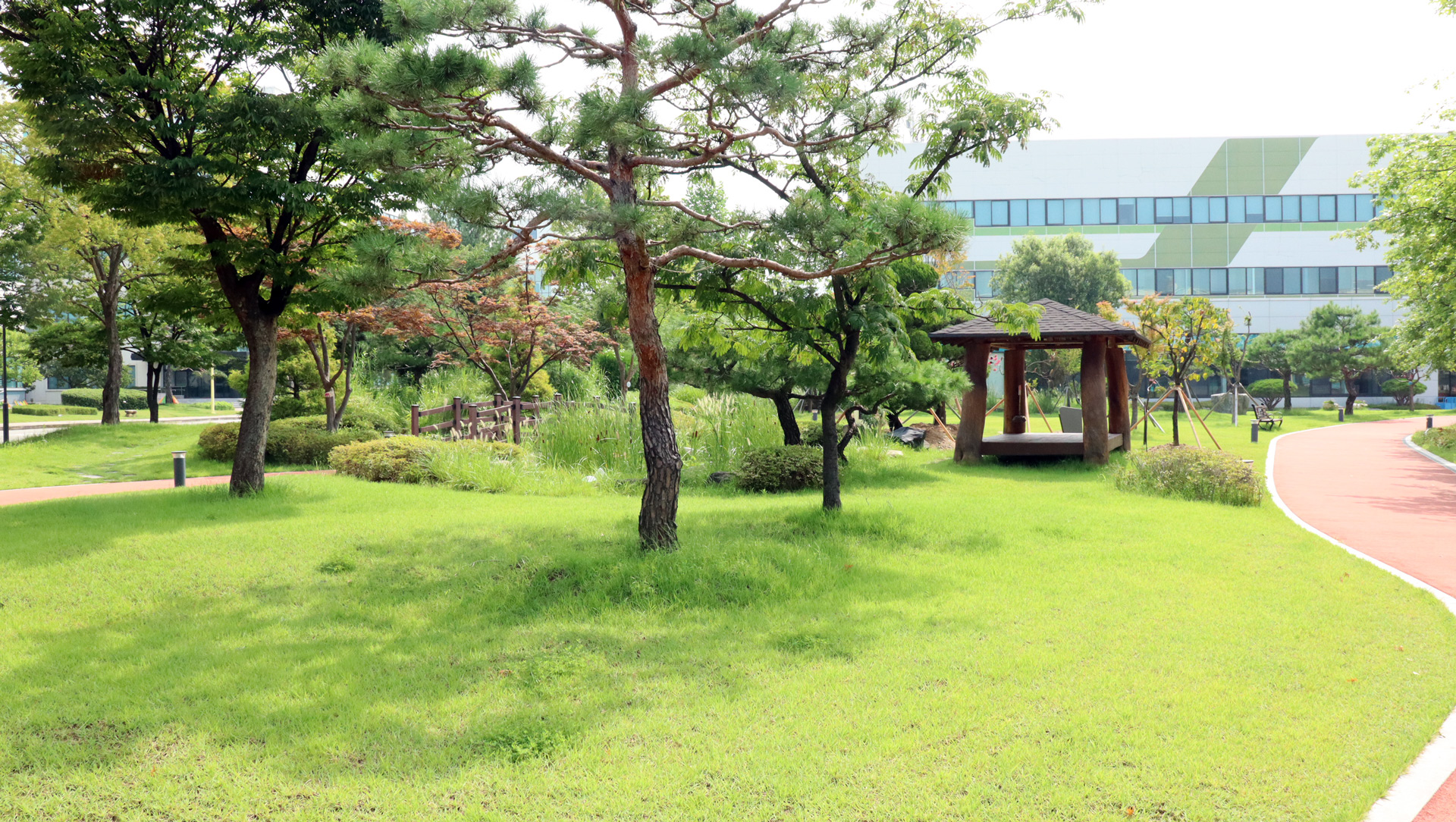
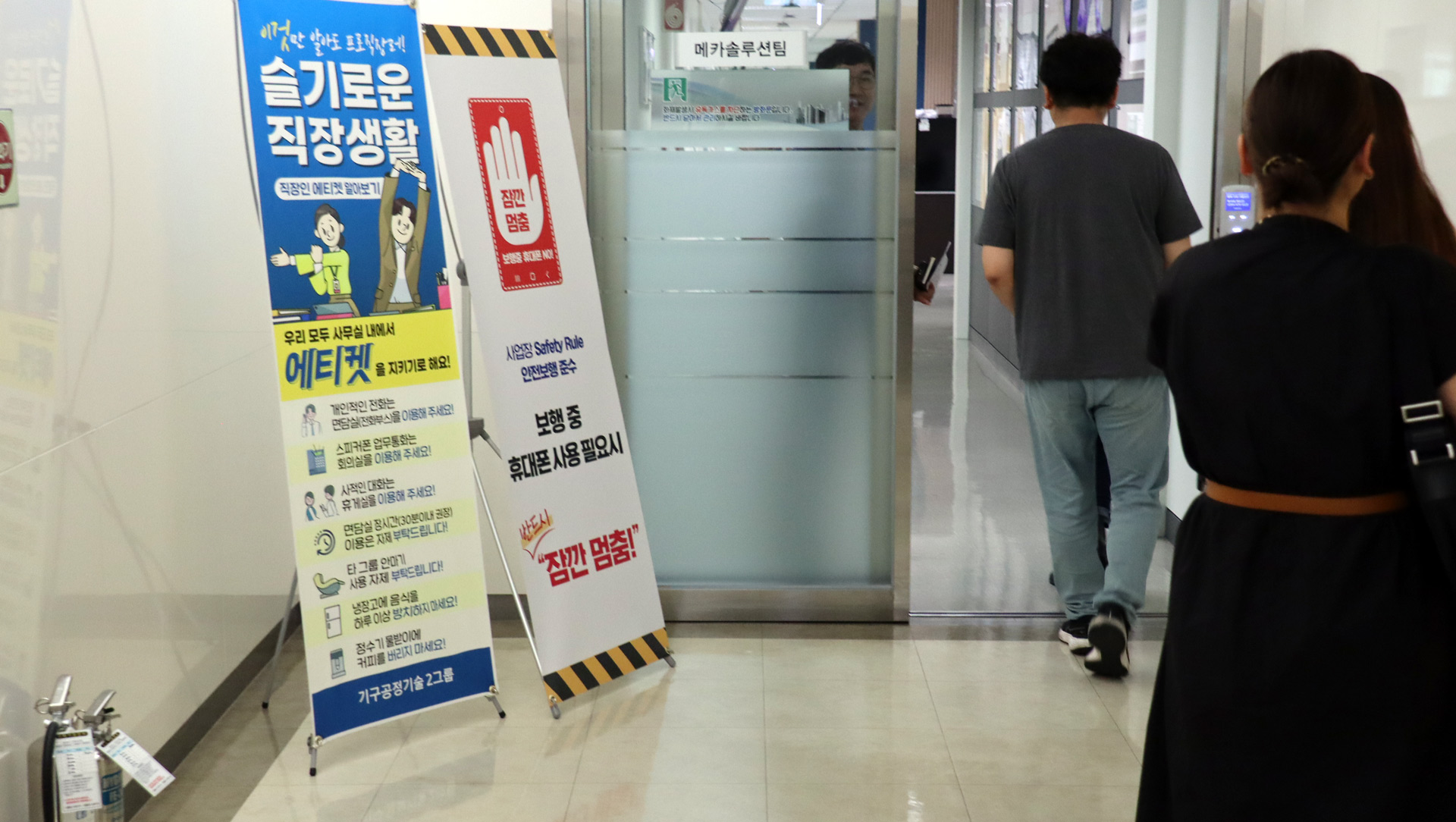
Let's get silicon rolling
We started our tour on the SMD line, a semi-clean room that works primarily on Printed Circuit Boards (PCBs) and the process of mounting and soldering components. PCBs sit at the heart of your smartphone, carrying, among other things, the brain (mobile CPU) and memory (RAM).
Before entering a corridor just outside the line, I stuffed my feet into a shallow white box that automatically slapped a pair of blue booties on my feet. The idea was to keep us from tracking in any debris from the outside world. I gingerly stepped through the sliding door and onto what appeared to be a floormat made of ball bearings. As my feet pressed the spring-loaded balls below the metal surface, a hidden vacuum sucked the remaining dust off our feet. I want one of these for my home.
I’m not sure what I was expecting to see on a smartphone manufacturing line, but it wasn't this: thirty, 40-meter-long lines of equipment (38 machines per line). Inside each box is an automated system performing a manufacturing task. There are almost no humans in the entire space. Samsung told me there is one person per line to make sure nothing breaks down and then one motion-keeper per every three lines to make sure things are moving properly between lines.
Essentially every stage in the intricate board printing, component, placing, and part soldering process is done by robots. Samsung has automated every bit of transferring and logistics. They did this, in part, as a response to COVID-19 where companies could not afford to have people working in close proximity to each other. Now it’s an essential part of how Samsung manufactures the best Samsung Galaxy phones.
Samsung showed us how one robot prints out a delicate, razor-thin, dual-side PCB while another takes 0.2-to-0.3mm components (you could fit thousands of these tiny components on a single US quarter), peels them off what looks like movie film reels, and carefully deposits them on the ultra-thin board. The stripped ribbons then snake back out of the small enclosure and flow into a nearby bin.
No one grabs the fragile boards and moves them to the next stage of the process. Instead, a series of unmanned, robotic vehicles carry the PCBs in rigid, protective jigs.
I’m not sure what I was expecting to see on a smartphone manufacturing line, but it wasn't this.
A PCB covered with components and solder beads then heads to an oven of sorts where the board is heated to 250 degrees Celsius and the tin, copper, and silver solder liquefies to fuse the components to the board.
After soldering, Samsung, or rather another robot, applies a resin to fix everything in place. It also uses a router to cut up the PCB. One full-size PCB can be broken up into between four and six smartphone motherboards.
Samsung tests and retests everything throughout the manufacturing process. In this case, it checks all the solder and loads up the finished PCB with system software. Things usually go pretty well along the line, which has roughly 500 failures for every 1 million units produced.
The entire process I just described takes under a minute.
It's a process
This, of course, was just the beginning. Naturally, the board has to go somewhere. Samsung took us down a flight of stairs, which we navigated carefully because all of us were still wearing our blue booties, to the second line where Samsung assembles, tests, and packages the phones – in this case a Samsung Galaxy S23 Ultra.
Unlike the PCB line, Samsung invited us inside to walk among the green boxes housing another collection of busy phone-building robots. Rolling between them and shuttling components and in-production phones from one robot to another is a small army of 50 slow-moving AGVs (automated guided vehicles). These rolling boxes moved carefully among the aisles, grabbing and depositing trays. Their sing-song toodles (designed I think to ensure the humans scattered throughout the production line could hear them coming) provided a nice counterpoint to the cool whirring of countless automatons.
There are 844 people working this line, though I found it hard to see many of them behind all the robot enclosures. For some reason, Samsung thought it was vital that we know the workforce demographics, explaining that the average age is 34, though most of the men are around 40 and most of the women are approximately 33. Half of them are married. More interestingly, the floor runs 16 hours a day with two 8-hour shifts and produces 2 million phones a month.
At Main Bay 05 and 06, we spotted a robot using a 3D scanner to check if connections are properly fastened. Nearby, another robot arm checked to see if it had the right board for the European or US markets. Once it’s done, another robot arm quickly fastens the proper connector.
My favorite though has to be the dual-arm robot station where one arm is responsible for removing a component’s protective film, while the second arm grabs the component off a rack and places it in the phone assembly. Watching the two arms work in tandem is like witnessing a talented, albeit headless and legless dancer. It’s efficient, elegant, and mesmerizing.
Above another enclosure is a series of translucent wells filled with tiny screws. The screws get vacuumed up and then shot down into position, where they can be screwed in place and then checked by a vision sensor.
Most robots have just one job, a task they can perform with near perfection over and over again. We saw one robot arm that, after one bot placed a protective coating on a screen for one process, failed to remove it before the phone could be shuttled along the assembly line. As a result, the system spit out the phone onto a tray where it joined the small group of NGs or “No Good” phones.
Later we watch as robots checked that the S23 Ultra’s S Pen is properly placed and functional, that NFC works, and even a quick test run of the system software. Samsung also tested the audio, radiation, and Wi-Fi waves, and even water resistance (using a water-free pressure test) in its quest to deliver functioning phones to you.
I realized I had literally just watched a Samsung Galaxy S23 Ultra come into being. It was like a birth, an automated birth.
I realized I had literally just watched a Samsung Galaxy S23 Ultra come into being. It was like a birth, an automated birth.
From here, the mid-wife AVGs delivered the finished products to a human for a final gut check and then to packaging.
Like everything else, the packaging is fully automated and employs some custom robot arms designed and built by Samsung. The packaging of each Galaxy phone is such a dance. I saw all the recognizable box and packaging parts flow through various sections of the enclosure and then come together to encase the phone. Packaging takes 9 seconds, far less time than it takes me to shoot an unboxing video.
Another Samsung robot started grabbing the packaged products and stacked the boxes together. However, when it had collected a half dozen boxes, the robot arm paused, switched tools, and then switched to the task of picking up the six boxes to place them in a larger box for palletization. All I can say is, that was cool.
Samsung Galaxy Folds and Flips are produced on this floor as well. Opposite the S23 Ultra line, a woman stood in a larger enclosure and used sticky translucent film to pull off any remaining dust from the screens of freshly-made Samsung Galaxy Z Fold 5 phones.
Overall, it’s a production line where very little ever goes wrong. The robots each know their task and perform them with almost silent efficiency. They do their quiet and thankless work to produce the smartphones we rely on. Humans are involved but mostly as managers, overseers, and cleanup crew for the rare job that a robot can’t handle.
This is how Samsung makes its sausage over and over again. It’s remarkable and all makes sense. I know I won’t be looking at my smartphone the same way again.
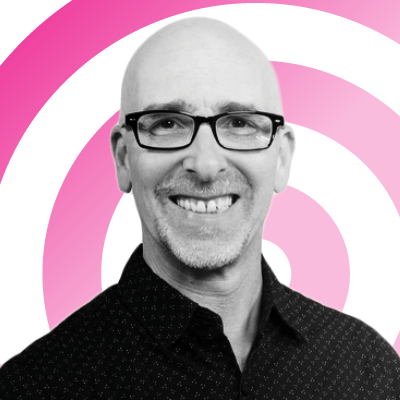
A 38-year industry veteran and award-winning journalist, Lance has covered technology since PCs were the size of suitcases and “on line” meant “waiting.” He’s a former Lifewire Editor-in-Chief, Mashable Editor-in-Chief, and, before that, Editor in Chief of PCMag.com and Senior Vice President of Content for Ziff Davis, Inc. He also wrote a popular, weekly tech column for Medium called The Upgrade.
Lance Ulanoff makes frequent appearances on national, international, and local news programs including Live with Kelly and Mark, the Today Show, Good Morning America, CNBC, CNN, and the BBC.