Here’s how gigacasting will make your next EV more affordable
What in the world is gigacasting?
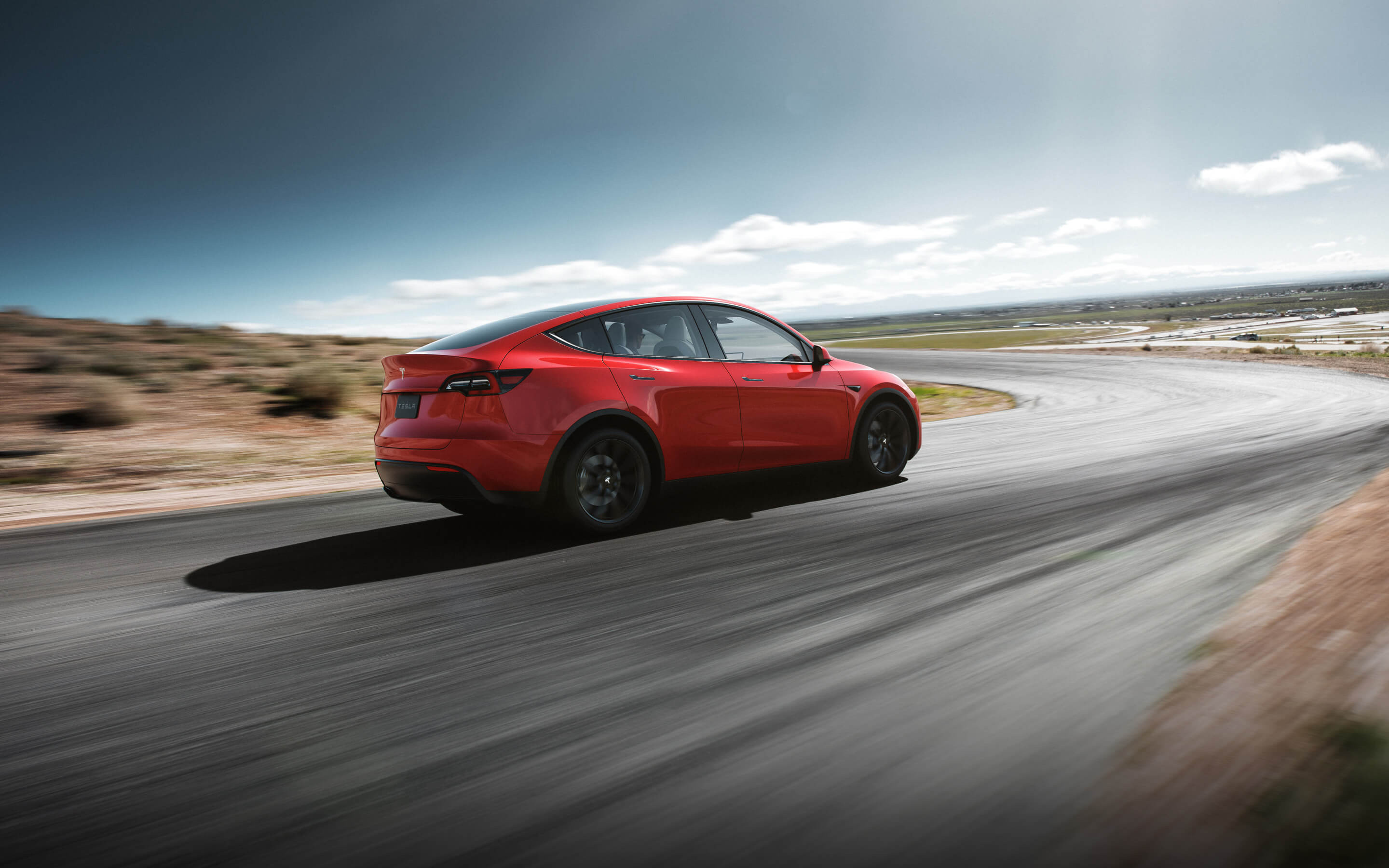
By now, you’ve probably heard about gigacasting, and how it’s being used by car manufacturers like Tesla, Toyota, Geely, and others for EV production. Gigacasting is a process that allows vehicle manufacturers to cast large parts in a single piece. For example, instead of building front and rear structures by stamping or casting a dozen (or more) separate parts, then welding, fastening, or bonding them together, these structures are cast as one big piece in a massive press or giga press.
Giga presses are basically high-pressure die-casting machines and are primarily designed and manufactured by the Italian company Idra Group. Each giga press is the size of a small house, weighs 400 tons or more, and can apply upwards of 6,000 tons of force, pushing an 80kg (180lbs) shot of molten aluminum into the casting mold at 10m/sec (33ft/sec). The yield is approximately 45 gigacastings per hour (or ~1000 per day).
Tesla pioneered gigacasting for EVs in 2020 and currently uses the technology to make the front and rear structures of the Tesla Model Y and the upcoming Cybertruck. In addition, the company is reportedly working on gigacasting underbody structures for next-gen cars. You can watch how cars are currently assembled and how Tesla will assemble upcoming EVs in the company’s recent Investor Day video. Obviously, Gigacasting makes this new manufacturing approach a lot more practical.
For its part, Toyota – the world’s number one carmaker, known for being a leader in manufacturing efficiency – is (finally) getting more serious about battery EVs, and has announced that it’s adopting gigacasting for its future EVs. Simultaneously, Japanese vehicle parts manufacturer Ryobi (yes, related to that Ryobi) has indicated that it’s planning to use gigcasting to reduce the cost of manufacturing car bodies by 20%.
Why will gigacasting upend the car industry?
Now, let's talk about how gigacasting will change the car industry in much the same way as electrification and software-defined cars did before it. Gigacasting is the logical next step in building vehicles – affordable EVs in particular – and is driven by economies of scale.
In a nutshell, gigacasting greatly streamlines vehicle manufacturing (shorter assembly lines, faster production), significantly reduces part counts (and storage/shipping), and enables increased modularity.
The cost savings associated with gigacasting either translate into higher profits in vehicles at the high end or offset the high price of batteries in EVs at the low end. Gigacasting also reduces weight and increases crash safety. Since there's no need to weld, fasten, or bond multiple structural parts anymore, vehicle design can be massively optimized. Basically, gigacasting is a win/win – a win for carmakers (profits and efficiency), and a win for consumers (price and safety). But what about repairability?
Get daily insight, inspiration and deals in your inbox
Sign up for breaking news, reviews, opinion, top tech deals, and more.
It’s true that gigacastings are almost impossible to repair. But is that a problem? Short-term, yes, but long-term, absolutely not.
It’s true that gigacastings are almost impossible to repair. But is that a problem? Short-term, yes, but long-term, absolutely not. You just need to think beyond how insurance companies, body shops, and vehicle recycling/refurbishing currently operate. Just like direct-to-consumer sales are in and dealerships are on their way out, service departments will become less relevant (because EVs require much less maintenance), and insurance companies and body shops are about to be upended.
Most body shops have done a poor job at embracing EV repair anyway – and that’s even before gigacasting comes into play. While lack of parts and training were an obstacle initially, that’s no longer the case. Like dealerships, body shops seem unwilling to evolve and adapt. Even though gigacasting makes structural repairs after a collision almost impossible, there are still plenty of opportunities for non-structural repairs (body panels, paint, trim, and glass).
Hidden benefits
Gigacasting lowers the risk of poor (and unsafe) structural repairs, which is a benefit to consumers. Since replacing gigacastings isn’t cost effective, damaged vehicles can be recycled instead. This opens up new recycling/refurbishing opportunities for vehicle scrap yards – a secondary market for non-structural parts to be used by body shops and service departments when doing non-structural or out-of-warranty repairs.
But what happens to the cost of insurance with gigacasting? In a post-EV world, car ownership makes little sense. Are you really planning to keep your EV – a smartphone on wheels – past the warranty period considering how fast technology is evolving? Leases/subscriptions are obviously the way to go. Then, the next logical step is for car manufacturers to offer their own insurance alongside the lease/subscription (like Tesla already does). This gives carmakers more control over what happens to a vehicle that needs repair.
Car manufacturers might even get involved in the recycling/refurbishing process. Insurance companies – like dealerships – aren’t a part of this future. Basically, you only have to look at what’s happening in the smartphone industry to understand where all this is going. Finally, gigacasting will enable a lot more design freedom for carmakers, so consumers will have more vehicle choices. The same gigacasting could be used for the front structure of a sedan, crossover, and small pickup truck, for example.
What gigacasting means for you
So what’s the takeaway here? Basically, just look at today’s Tesla Model Y, which keeps dropping in price. In the next year or two, it’s likely that your next EV will become a lot more affordable. It will also be more difficult to repair after a collision. EVs will continue to evolve quickly, so you’ll be leasing yours, with the insurance being provided by the manufacturer. And to keep prices at bay, you’ll likely be “purchasing” that EV directly from the manufacturer, without any egregious dealer markups and costly visits to the service department.
Frankly, that’s a win in my book.
You might also like
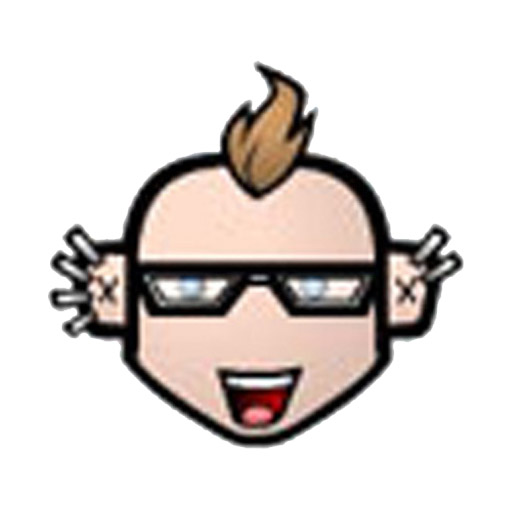
Myriam Joire (tnkgrl) was born wearing combat boots and holding a keyboard. Moments later she picked up a soldering iron. On weekends, she rally-raced with her father. She's been stomping, typing, hacking, and driving ever since. After spending years being a code-monkey in the video game industry, she joined Engadget as Senior Mobile Editor and later Pebble as Chief Evangelist. Today she hosts the weekly Mobile Tech Podcast, makes videos on YouTube, writes about tech and cars for TechRadar and other major publications, and advises startups on product/media strategy. She's based in San Francisco.